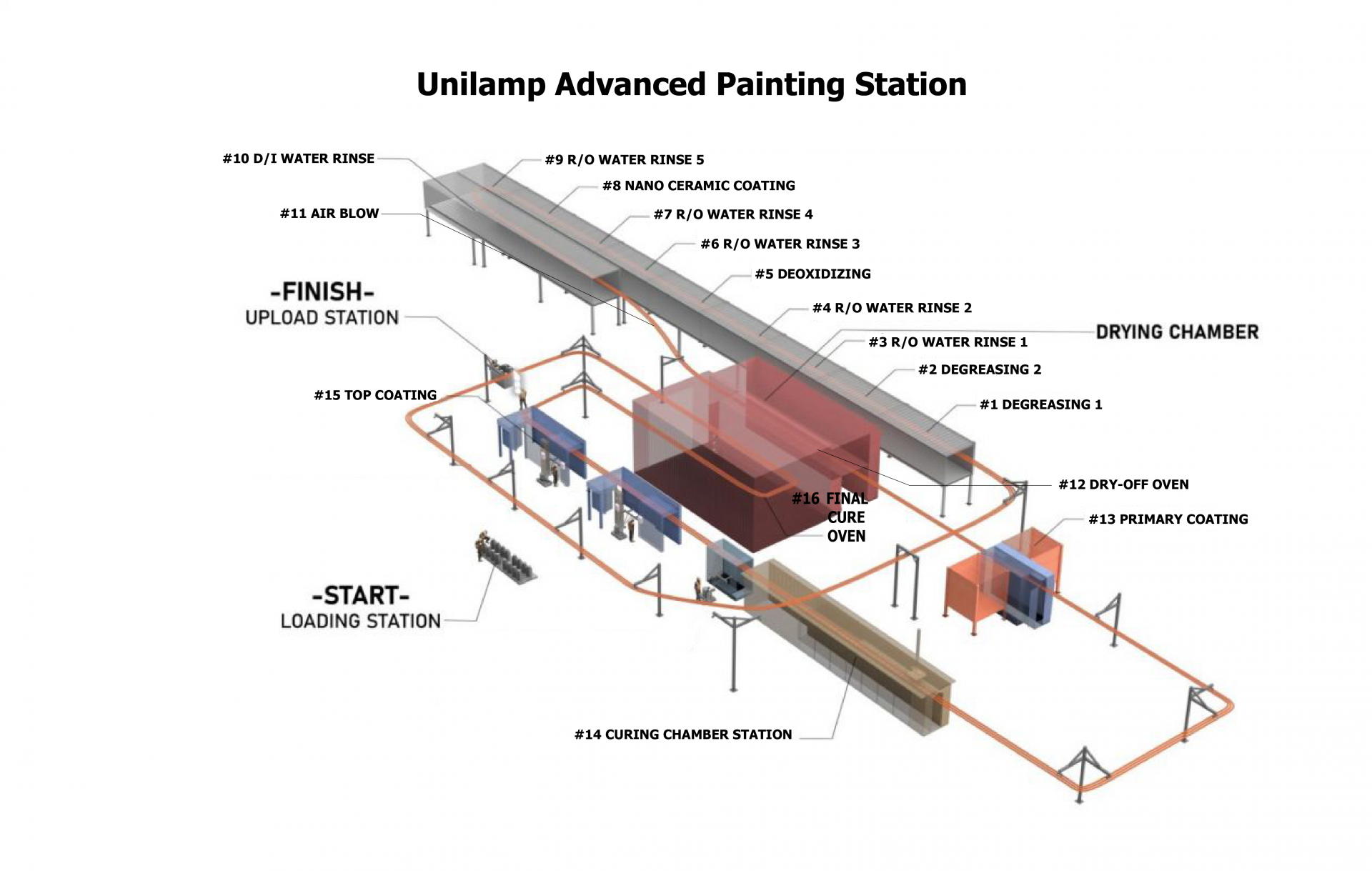
The 16-Stage UniShield16 Coating Process
What is UniShield16?
UniShield16 is Unilamp’s advanced coating system, providing long-lasting protection, superior durability, and aesthetic excellence for every luminaire. Designed to withstand demanding conditions, this 16-stage process enhances corrosion resistance, color consistency, and surface durability. The process ensures optimal performance and longevity, with three-coating-layer system of UniShield16’s exceptional resilience.
The 16 Stages of UniShield16 Coating
Stage 1 – Stage 7 : Surface Preparation and Cleaning
These initial stages ensure the fixture’s surface is clean and prepared for the application of the coating layers.
- Stages 1–2 : Degreasing: The fixture is cleaned to remove oils, lubricants, and residues from manufacturing.
- Stages 3–4 : RO Water Rinsing: Using reverse osmosis water, any remaining contaminants are removed to ensure a clean, neutralized surface.
- Stage 5 : Deoxidizing: The metal is treated to remove natural oxide layers, exposing fresh metal for improved bonding.
- Stages 6–7 : Final Rinsing: After deoxidizing, thorough rinsing ensures that all residual chemicals are removed, preventing any surface contamination.
These preparation steps ensure the fixture's surface is completely clean and chemically stable, setting the stage for optimal adhesion of the coating layers.
Stage 8 : Nano-Ceramic Coating, The Core of UniGreen Protection
Nano-Ceramic Coating is the first key layer applied to the fixture, central to UniShield16’s performance. This environmentally responsible layer uses advanced nano-ceramic technology, which enhances corrosion resistance, chemical bonding, and surface durability.
Key Benefits:
- Eco-friendly: Free from toxic chromates, supporting sustainable practices under the UniGreen initiative.
- Corrosion Resistance: Provides superior protection in high-exposure environments like coastal and industrial areas.
- Bonding Enhancement: Promotes better adhesion of the subsequent primer and topcoat layers, ensuring a long-lasting finish.
This stage is essential for ensuring robust corrosion resistance and a solid foundation for the subsequent layers.
Stage 9 – Stage 10 : RO and DI Water Rinse
- Stage 9 : RO Water Rinse: Balancing the Nano Layer Excess nano-ceramic solution is carefully rinsed off to ensure an even, consistent pre-treatment layer. This step prevents future issues such as blistering, cracking, or adhesion failures, ensuring long-term performance.
- Stage 10 : DI Water Rinse: Deionized (DI) water, free of minerals and ions, is used for the final rinse. This step removes any remaining impurities, preventing spotting or chemical reactions that could affect the quality of the finish. It promotes a spotless, flawless result.
Stage 11 – Stage 12 : Moisture Removal and Surface Drying
- Stage 11 : Air Blow Station: High-pressure air jets are used to remove residual water from the fixture after DI rinsing. This step targets hidden areas and complex geometries, ensuring no moisture remains trapped before entering the drying oven.
- Stage 12 : Dry-Off Oven Station: The fixture passes through a controlled-heat oven to fully evaporate any remaining moisture. This ensures the surface is completely dry and ready for coating, reducing risks of bubbling, pinholes, or coating defects.
Key Benefits:
- Ensures that water does not accumulate in recesses or intricate parts of the fixture.
- Prevents moisture-related defects such as bubbling or poor coating adhesion.
- Increases process efficiency by reducing drying time in the next stage.
Stage 13 – Primary Coating Station: First Layer of Protection
The Anti-Corrosive Primer is applied as the second key layer. This primer forms a strong bond between the nano-ceramic layer and the topcoats, enhancing mechanical strength and corrosion protection. It significantly improves the fixture's resilience against impacts, scratches, and micro-cracks.
Key Benefits:
- Improved Bonding: Ensures strong adhesion between the nano-ceramic layer and the final topcoats.
- Mechanical Durability: Increases the fixture’s resistance to physical damage and environmental stress.
- Corrosion Protection: Acts as an additional barrier against rust and other environmental factors.
Stage 14 – Curing Chamber Station: Heat-Fusion of Base Coat
The fixture is placed in a high-temperature oven to cure the primer. This thermal curing process chemically bonds the primer to the substrate, enhancing its resistance to peeling, cracking, or fading. The base coat is now firmly adhered and ready for further protection.
Stage 15: Top Coating Station
Enhanced Protection Layer: polyester topcoat reinforces the UV and weather protection, enhancing the fixture’s overall durability.
Key Benefits:
- UV Protection: Prevents discoloration and degradation due to sunlight.
- Aesthetic Quality: Provides a smooth, glossy finish that retains its appearance for years.
- Enhanced Durability: Protects against environmental wear, ensuring long-term performance.
Stage 16 : Final Curing, Locking in Durability
In the final stage, the fixture undergoes a high-temperature curing process, which bonds all the layers together into a unified, durable finish. This step ensures the complete fusion of the nano-ceramic coating, primer, and polyester topcoats, resulting in a highly resilient, corrosion-resistant surface.
Key Benefits:
- Permanent Bonding: Ensures the longevity and stability of all coating layers.
- Surface Durability: Locks in protection against the elements, providing superior performance under demanding conditions.
Why 16 Stages?
The 16-step process is essential for ensuring that each fixture receives the maximum level of protection and durability. Each stage is carefully designed to optimize adhesion, corrosion resistance, color retention, and surface integrity. The process combines cutting-edge technology, eco-friendly materials, and precise application techniques to create a highly resilient and long-lasting finish, all while aligning with UniGreen – Lighting the World, Sustainably for All.
Standardized Quality Control for UniShield16
UniShield16 is engineered to meet Unilamp’s highest performance and sustainability standards. Every luminaire coated with UniShield16 is subject to a strict, standardized quality control protocol—developed to ensure consistent coating integrity, environmental resistance, and long-term reliability.
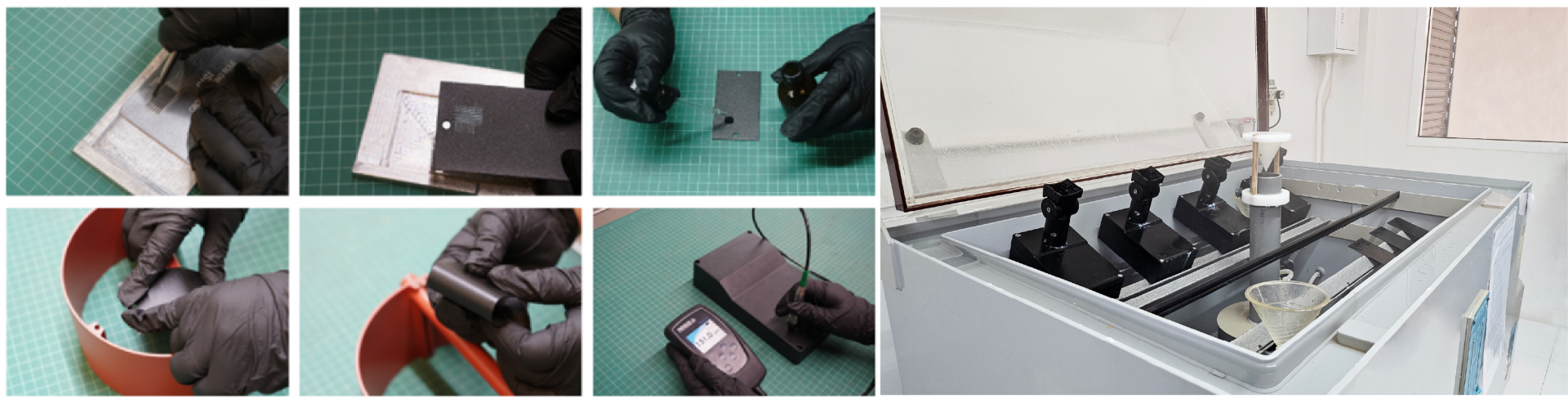
Unilamp’s Quality Assurance for UniShield16 includes:
Controlled 16-Stage Coating Process
Each luminaire undergoes a fully controlled process from pre-treatment to final cure, ensuring consistency and optimal layer performance.
Advanced Testing Protocols
We perform comprehensive testing beyond industry requirements, including:
- Film Thickness Control to ensure precise 120-micron layering.
- Adhesion & Flexibility Tests to prevent cracking, peeling, or delamination.
- Corrosion Resistance (Salt Spray & Humidity Tests) for long-term performance in harsh environments.
- Chemical Resistance to safeguard against pollutants and industrial exposure.
- UV and Weathering Tests for lasting visual and structural integrity.
Uniformity & Aesthetic Evaluation
Every surface is inspected to ensure flawless finish, color consistency, and gloss retention—essential for architectural lighting standards.
Certified to Global Standards
UniShield16 is developed and tested in alignment with internationally recognized standards, ensuring exceptional performance, safety, and sustainability. These certifications reflect Unilamp’s commitment to engineering excellence and environmentally responsible manufacturing under the UniGreen initiative.
- Green Industry Level 3 Certification: Recognizes Unilamp’s sustainable production practices, supporting reduced environmental impact in line with Thailand’s green industry framework.
- ISO 9001 and ISO 14001 Certifications: Demonstrate Unilamp’s rigorous quality management and environmental stewardship across all stages of product development and manufacturing.
- ISO 45001:2018 Certification: Affirms Unilamp’s commitment to occupational health and safety standards in every process, from coating to assembly.
- IEC 60598, CB Test Certificate, and ENEC Certification: Verify that Unilamp’s lighting products comply with international safety and performance standards for electrical equipment.
- VDE – Approved Place of Manufacture: It indicates that Unilamp’s production processes, quality-control systems, and in-house testing facilities are regularly audited by VDE.
These certifications position UniShield16 as a vital part of Unilamp’s globally trusted lighting solutions, delivering performance and reliability in the most demanding environments.
Through rigorous quality control and the UniGreen initiative, Unilamp ensures that UniShield16 provides lasting durability, sustainability, and peace of mind—trusted by lighting professionals worldwide.
For more information, visit www.unilamp.co.th or contact online@unilamp.co.th